Renewing the Process Control Extends the Lifespan of a Particle Accelerator
The nearly 30-year-old control system of the particle accelerator in the University of Jyväskylä was in need of renewal to support the future needs of the facility, and Rockwell Automation from Klinkmann was chosen as a partner for this exceptionally extensive project.
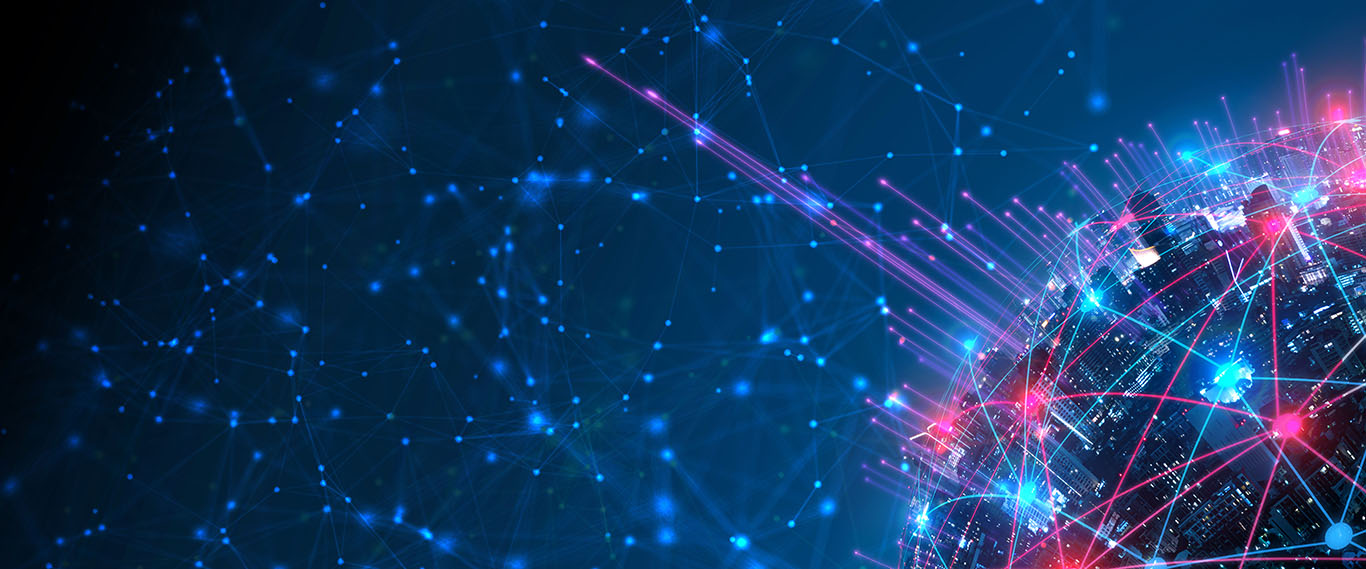
How to secure continued reliability and modernize operations in one of Europe’s largest particle accelerator laboratories? That was the key question The University of Jyväskylä’s Department of Physics had to find an answer to.
Department of Physics operates one of Europe’s largest particle accelerator laboratories, a key research facility used by global organizations such as the European Space Agency.
The lab renewed its nearly 30-year-old control system. Rockwell Automation, delivered by Klinkmann, was selected for this complex project involving around 2000 I/O points. Klinkmann's solution included everything from I/O cards and cabinets to servers, software, and comprehensive training.
The upgrade was completed in summer of 2020.
Comprehensive solution to an aging accelerator
Due to the laboratory’s continuous 24/7 operation and minimal downtime tolerance, the transition required precise planning and staged commissioning.
One of the key drivers for the upgrade was the declining availability of spare parts for the old system.
The new system offers high reliability, easy maintenance, and customizable user interfaces tailored to the lab’s unique needs. The partnership with Klinkmann was praised for its flexibility, responsiveness, and problem-solving approach, ensuring the successful modernization of a facility crucial to scientific research and innovation.
Klinkmann can definitely be recommended to companies planning to renew the entire system or its parts.